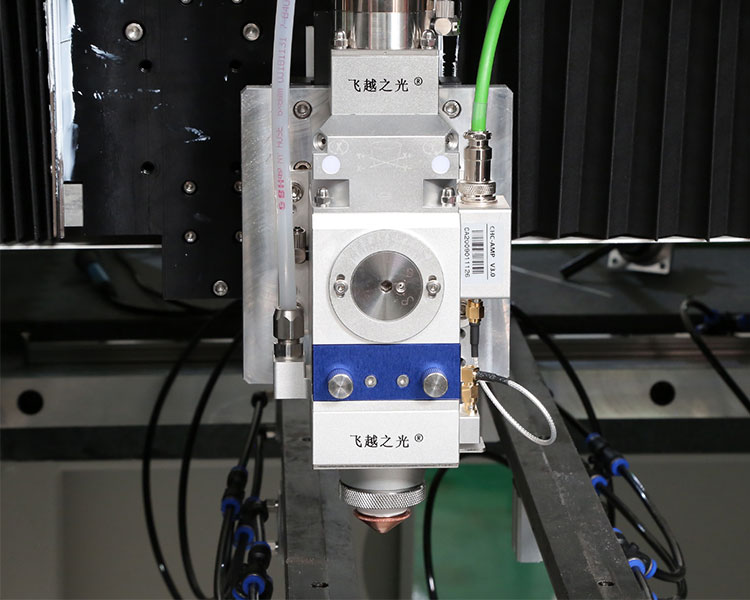
The components of the laser cutter head of the laser cutting machine are: nozzle, focus lens and focus tracking system.
Laser Nozzle
The choice of nozzle form and nozzle size has a great influence on cutting quality. There are three main types of nozzles: parallel, convergent and conical. Such as the overview diagram. However, some foreign institutions have applied the knowledge of aerodynamics to develop a convergent-expanding nozzle. This type of nozzle can have good cutting characteristics when used in cutting. However, due to the complicated inner cavity of the nozzle, the processability and fineness of the processing are limited, making it impossible to put into industrial production.
Focusing lens
To use the energy of the laser beam to cut, the original beam emitted by the laser must be focused by a lens to form a high-energy-density light spot. According to Gaussian optics theory, the power density is the highest at the focal point. The longer the focal length of the lens, the larger the focal spot and the lower the power density, but the greater the focal depth (the focal depth refers to the distance between the two spots with a 5% change in diameter on both sides of the focal point, which is also called the effective cutting range during cutting), and the operating tolerance Big. The effective range of a 5-inch lens is larger than that of a 3-inch lens. This is why it is said that the medium-telephoto lens is suitable for thick plate cutting, and has low requirements for the pitch stability of the tracking system, but requires high laser output power. On the contrary, the short focus lens is only suitable for thin plate cutting below D3. Short focus has strict requirements on the pitch stability of the tracking system, but its requirements on the output power of the laser can be greatly reduced.
Tracking System
The focus tracking system of a laser cutting machine is generally composed of a focus cutting head and a tracking sensor system. The cutting head includes light guide focusing, water cooling, air blowing and mechanical adjustment parts; the sensor is composed of sensing elements and amplifying control parts. The tracking system is completely different according to the different sensing elements. Here, there are mainly two types of tracking systems, one is the capacitive sensor tracking system, also known as the non-contact tracking system. The other is an inductive sensor tracking system, also known as a contact tracking system.
Failure And Repair
Electrodes and nozzles are the most consumed consumables in the daily operations of CNC plasma cutting machines and laser cutting machines, especially the imported electrodes and nozzles. Therefore, effectively extending the service life of electrodes and nozzles will greatly reduce the production cost of plasma cutting. The consumption of electrodes and nozzles is related to various factors such as air pressure, cooling water pressure, voltage, current, air supply quality, and the quality of consumable parts. It is also necessary to pay attention to some abnormal consumption caused by machine failures. I have encountered the phenomenon that the complete set of electrodes and nozzles were frequently burned at the moment the cutting machine started the arc, and some burned within 0.5~1h after cutting. These are not normal consumption.
After inspection, it was found that the arc generated between the electrode and the nozzle sintered the edge of the electrode and the nozzle. For this reason, measures such as the use of different types of electrodes and nozzles, replacement of new cutting guns, and adjustment of air and water pressures have been adopted. Although the effects have changed somewhat, they are not significant, and they sometimes return to normal inexplicably.
After repeated inspection, it was found that the fault was caused by accidental loss of air during the cutting process. Sectional investigation found that the solenoid valve in the electric valve console was de-energized and the gas was cut off, and the solenoid valve was de-energized due to the torch trolley dragging back and forth, resulting in poor contact of the torch control cable. Due to the short time when the air is cut off, it is good when it is to be measured, and it is difficult to find faults. It was during this very short period of time that the electrodes and nozzles were burnt. After repairing the fixed cable again, the fault is eliminated.
Looking For Powerful Laser Cutting Machine?
Choose Feiyue,Choose Core Advantages
More Than 40 Independent Research Development Patents